What is the Price of Self-Leveling Concrete?
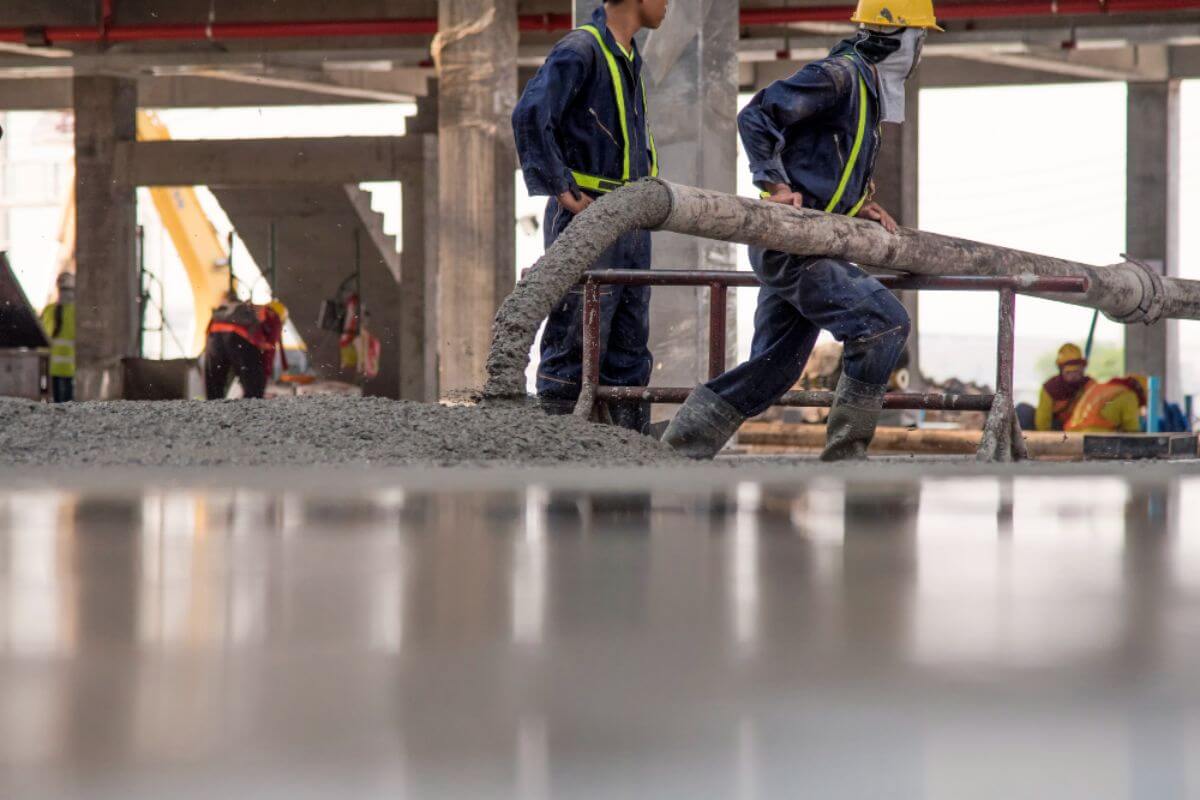
What factors affect the self-leveling concrete price?
- Material costs
- Brand and quality
- Area of coverage
- Complexity of the job
- Labor costs
- Shipping and transportation
- Environmental factors
Overview
- Flawless floors in commercial spaces create a professional and polished atmosphere.
- Self-leveling concrete ensures smooth, professional floors.
- Material quality, brand reputation, project size, job complexity, labor expertise, and transportation all influence self-leveling concrete prices significantly.
First impressions matter, especially in commercial spaces. A flawless floor creates a professional and polished atmosphere for clients and employees. Self-leveling concrete provides the perfect solution for a smooth, level surface that enhances the property’s overall look.
However, the cost varies significantly. This article explains the key factors influencing self-leveling concrete prices, helping building owners and contractors make informed decisions, stay within budget, and achieve a stunning floor that elevates the entire space.
Material Costs
Specialty self-leveling cements designed for specific applications, such as those with faster drying times or increased durability, tend to be more expensive than the standard ones. These higher-quality mixes offer improved performance, making them suitable for projects that require exceptional strength or moisture resistance.
Aggregates, such as sand and gravel, also play a role in the overall cost. Finer aggregates are generally less expensive than coarser aggregates However, the specific mix design may necessitate the use of a certain type or size of aggregate, which can impact the final price.
Various additives such as plasticizers, accelerators, and fibers can influence the cost. Specialized or high-performance additives designed for challenging environments, like high-traffic areas or exterior use, are typically more expensive than standard additives.
Brand and Quality
Reputable manufacturers invest heavily in research and development to create self-leveling concrete mixes with superior features, such as better flow, enhanced leveling properties, and increased strength. These specialized additives and processes contribute to their higher price points.
Despite the cost, many customers are willing to pay more for self-leveling concrete from trusted brands. They know these products will deliver consistent, high-quality results. Additionally, well-respected brands often offer better technical support, warranty coverage, and customer service, making the higher price worthwhile.
Area of Coverage
The size of the area that needs to be covered with self-leveling concrete can significantly impact the overall project costs. As the square footage increases, the amount of material required will also grow. However, this can potentially lead to economies of scale, resulting in lower per-unit costs.
As the project scale expands, fixed costs like delivery fees and setup expenses can be spread across a greater volume of material. This results in a lower per-square-foot price for the self-leveling concrete. Contractors and businesses working on larger installations may use this to negotiate better rates from suppliers, further driving down the per-unit costs.
Complexity of the Job
Projects with extensive surface prep, hidden structural issues, or unusual layouts require more time and effort. These additional steps often involve specialized skills and equipment that aren’t part of a standard floor installation. Think of it like this: the more intricate the groundwork, the more a smooth finish costs.
If a floor area includes structures like columns, stairs, or transitions, applying self-leveling concrete becomes more challenging. Contractors must carefully fit the material around these features, requiring more time and expertise. Also, irregular floor shapes, such as rooms with angled walls or non-rectangular layouts, complicate the installation. Specialized techniques, tools, and additional manpower are needed to ensure a seamless, uniform finish, which increases the project’s costs.
Labor Costs
Labor costs are a crucial component in the budgeting of self-leveling concrete installations. They encompass a spectrum of tasks, beginning with the thorough preparation of the substrate and extending to the meticulous finishing touches required for a flawless surface.
Every aspect of the process requires specialized skills, tools, and techniques. Contractors prioritize highly skilled labor for these projects, particularly those with precise requirements or tight timelines. Consequently, the costs incurred are a reflection of the expertise needed to deliver a perfectly polished result that aligns with client demands.
Shipping and Transportation
Projects in remote areas face higher transportation costs due to increased fuel expenses and delivery fees from longer distances. Conversely, sites closer to suppliers incur lower costs because materials arrive more quickly and easily.
How you receive supplies also impacts costs. Bulk deliveries by truck or freight are generally more budget-friendly than multiple smaller shipments. However, using specialty vehicles like concrete trucks can add extra expenses.
A little strategic planning with your self-leveling concrete supplier can go a long way in keeping your transportation costs in check. By factoring in location, distance, and logistical details, you can make smart choices that optimize your budget while guaranteeing a smooth pour.
Key Takeaway
Understanding the key factors affecting self-leveling concrete prices allows contractors to compare the features, quality, and pricing of different brands. This helps them find the best value and select a cost-effective, reliable supplier for their flooring projects.
With our extensive knowledge and cutting-edge techniques, Flooring Solutions is your go-to ally for exceptional flooring services. Contact us today and let us guide you through the process of transforming your floors into a stunning and functional asset.